Behind the scenes: Parachute Bay
At the end of an exercise or operation the Royal New Zealand Air Force team at Safety and Surface ensure all equipment is properly inspected, up to scratch and packed away properly. It can sometimes take weeks of work.
15 June, 2022
We visited the Cargo Aerial Delivery Equipment (CADE) bay at Base Ohakea following a major No. 40 Squadron airdrop exercise in the area. The biggest parachute the unit works with, the G-11, has a 100 foot (30m) and 120 gore canopy. A gore is the area of the canopy between each rigging line from the base to the top in the shape of a triangle. Each gore is then divided into a number of panels.
The huge mass of material is being inspected for any damage such as tears, holes or friction burns, before it is folded properly and stowed into its deployment bag.
A fan is being used to inflate the canopy, making any damage easy to spot.
“The big parachute can carry up to 5000 pounds (2300kg),” Safety and Surface Co-ordinator Flight Sergeant (F/S) Forrest McLeod said.
They range from 100ft canopies to 68 inch (1.7m) pilot chutes. The smallest parachutes are the T-7As, which were developed by the Air Force utilising ex-ejection seat parachutes, and are used for tasks including mail drops to scientists based at Raoul Island.
Safety and Surface personnel check over parachutes after an exercise
Once used the parachutes are delivered back to the bay where the team can spend between an hour and a day untangling and hanging them, ready to be inspected.
“When it’s dropped and released it can turn into a big mess depending on the wind conditions. When you’ve got drop zones like Raumai Range, or they’re dropped in a paddock, they can collect a lot of debris, which we’ve got to shake out,” F/S McLeod said.
“We’ll hang them up and shake them out and get all the sheep poop, pines cones and grass out of them and then bring it into the bay here. Depending on the drop zone it could be full of sand or it could be on dewy grass and they get a bit wet.”
The high-ceilinged wash tower, where the parachutes are hung from a height of 23m, has copper pipe showerheads, which enables the washing out any debris or rinsing out salt water from the canopies.
“It’s warm in there because there is a dehumidifier working that helps to dry them. You can’t force dry them, but we can speed the drying process along. The walls are all cladded and insulated to also help with the drying process,” F/S McLeod said.
The room is multi-purpose and is used by other Safety and Surface units throughout the base and Fire Flight, to wash and dry equipment.
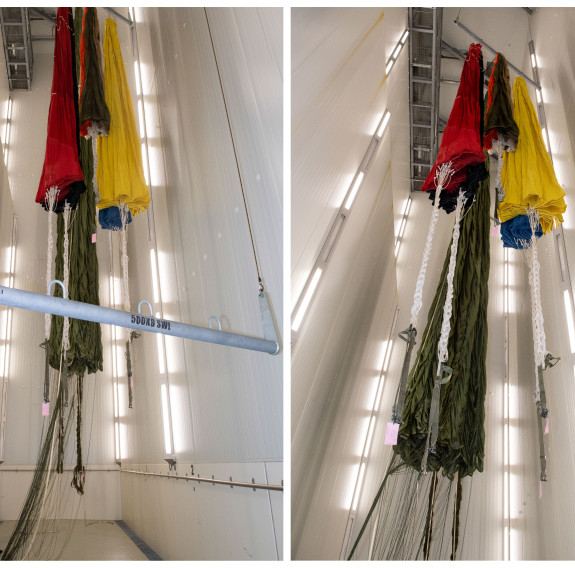
The high-ceilinged wash tower at the S&S parachute bay
Aerial Delivery Bay repair technician Bruce Mulcock said the largest parachutes (G-11) weighs 120kg when they are packed. Stretched out, with the canopy, 120 rigging lines and nine tapes the entire parachute reaches 160ft (nearly 49m) in length.
The worst tangle Mr Mulcock found himself sorting out took three and a half weeks.
“Once we had some come back from a pine plantation and the whole place smelled like pine – it was really good,” he said.
There are a couple of parachuting aspects to the load coming out of an aircraft, firstly there’s the extractor chute that pulls the load out from the aircraft and then initiating the deployment of the parachute or parachutes attached to the load. It’s really impressive to watch –these parachutes look like a big jellyfish floating down.
Cargo parachutes are a New Zealand Army capability, because of the airworthiness standards within the Air Force, F/S Mcleod said.
“It’s our responsibility to store and maintain all parachute assemblies in the CADE bay. The Army’s 5 Movements Company is responsible for the rigging of all loads, including the parachutes dropped from our aircraft, and will request the number and type of parachutes required for equipment or supply dropping tasks.”
Along with using the parachutes to drop supplies on land, they are also used to support dropping operations over water such as NZSAS Amphibious operations and training.
The unit also supports humanitarian aid and disaster relief missions, so they always need a certain number of parachutes packed and ready for issue at any given time.
If that’s not enough, the team is also responsible for the manufacture of the Minimum Aid Delivery Device (M.A.D.D), used to drop minimal survival aids or radios to stricken sailors as part of No. 5 Squadron and No. 40 Squadron’s search and rescue capability.